Infinite
Infinite is a stationary organisation system designed for both functionality and aesthetics. It is marketed towards 25- to 35-year-olds who work from home and intend to use it in a home-office environment. The target market can be further narrowed to those who are more environmentally conscious and are willing to pay at a higher price point for such goods. A key focus is therefore placed in the use of high-quality materials and sustainable manufacturing methods. The design is also intended to appeal to people who desire a visually appealing workspace. The holder should complement the aesthetic of their desk, whilst creatively serving its functional purpose of holding and storing stationary.
Ideation Phase
Based on the design intent, I began developing ideas through sketching. I focused primarily on the form of the product with the purpose of developing a holder that was visually interesting. It was essential that I did not let my preconceptions of the properties of wood hinder the ideation stage. The image below showcases the various forms explored (chosen idea is circled).
I then began researching into manufacturing techniques that could be used to achieve the curved form. ‘Bendy Ply’ was chosen as the construction material. It is a non-structural lightweight plywood with increased bending properties. Differing from regular plywood, the grains of each layer of laminate are aligned. This allows for the ply to bend with great flexibility along the grain to achieve tight curves. Research further revealed that bendy ply with low formaldehyde content and FSC or PEFC certified ply can be sourced to meet the sustainability objective of the project.

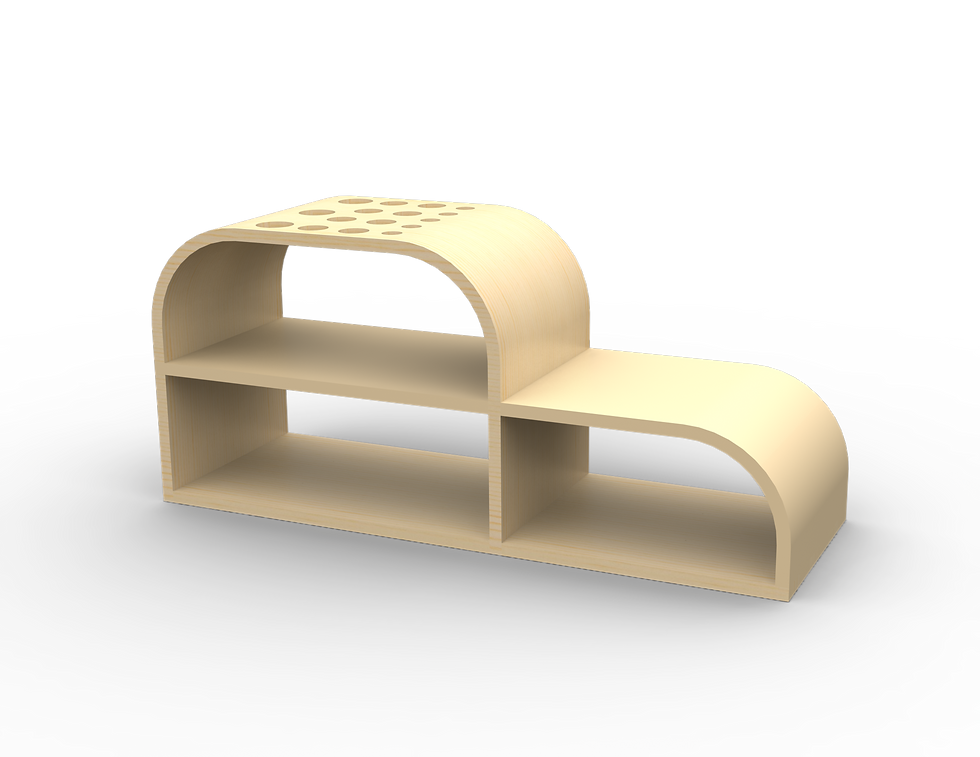


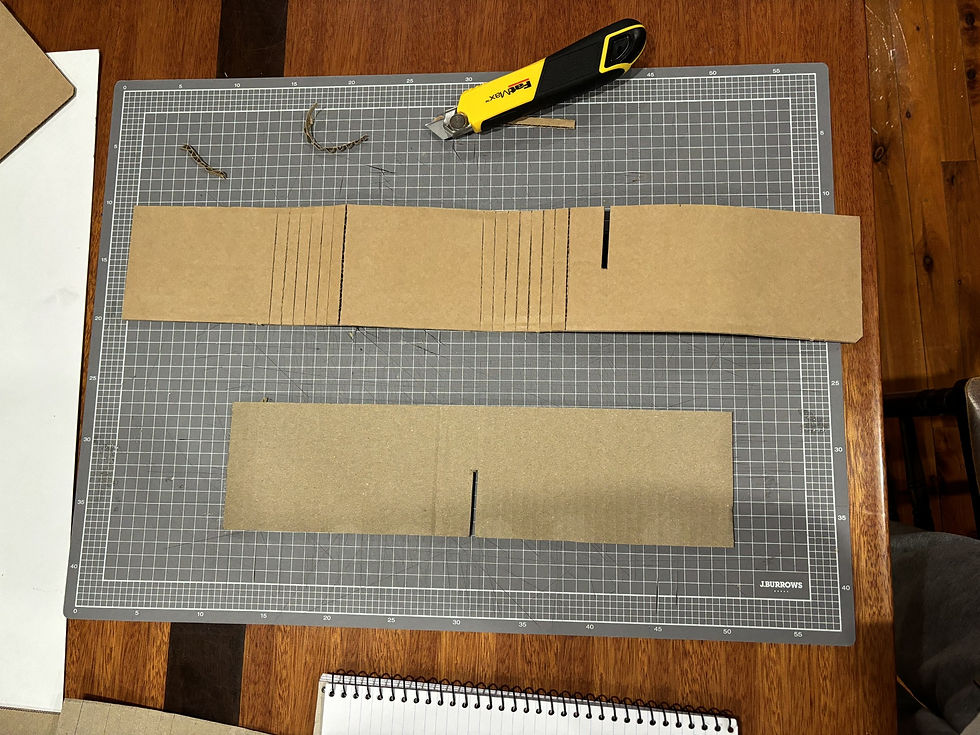

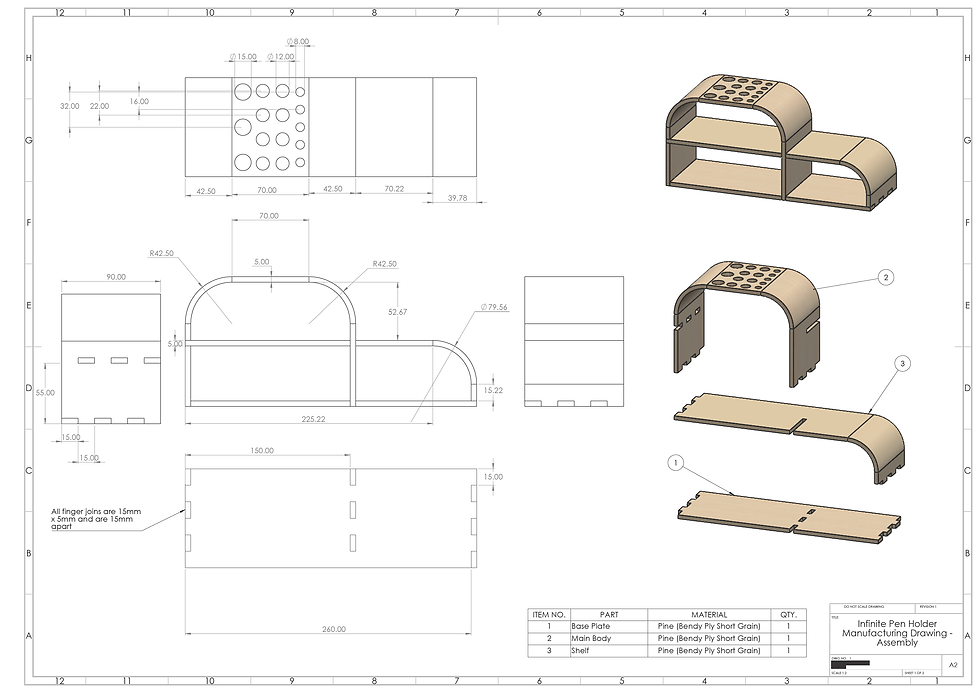
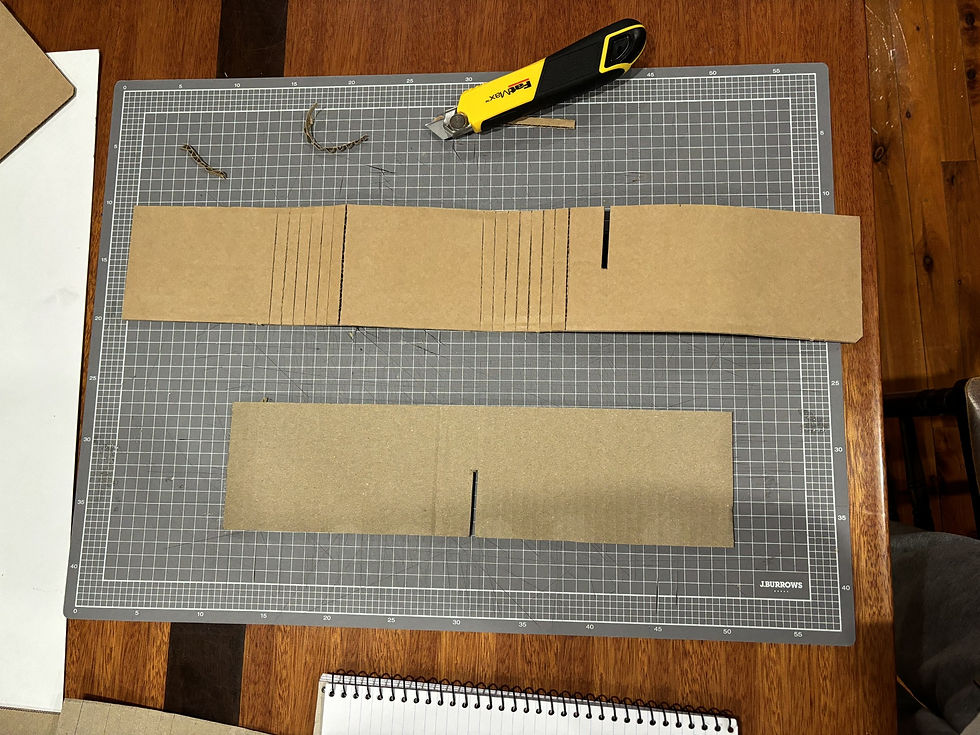
Prototyping and CAD
Cardboard prototyping was then completed to establish a sense of scale and suitable connection methods for the design. The prototype was initially designed to be a two-piece design and connected through friction fit. A cut through half of the width of each piece is used to create a seamless connection. Furthermore kerfing was used along the curved points of the design to aid with the material's bending.
The model was then recreated in Solidworks. The intention is to provide both visual aid through renders and allow translation into code for CNC machining. It is to be noted that the renders feature a three part design, differing from the cardboard prototype. The change is due to issues experienced when modelling with the 'bendy ply'. The curve could not be achieved without cracking of the material requiring for the design to be adjusted. Working drawings of the design are also showcased on the final slide.
Woodworking
The CAD model was then used to create SVG files which could be implemented into 'Carbide Create'. The software was then used to send code to a CNC to precisely cut the wood to the correct dimensions. The stage required a lot of adjustments to achieve the final form due to issues with breaking when bending the ply. Initially, it was intended that half-cuts would be made along the curved points of the model. The technique however did not allow for enough flexibility, leading to cracking of the wood. The product eventually evolved to utilising a honey-comb kerfing method. The method provided increased flexibility, allowing for completion of the final product.
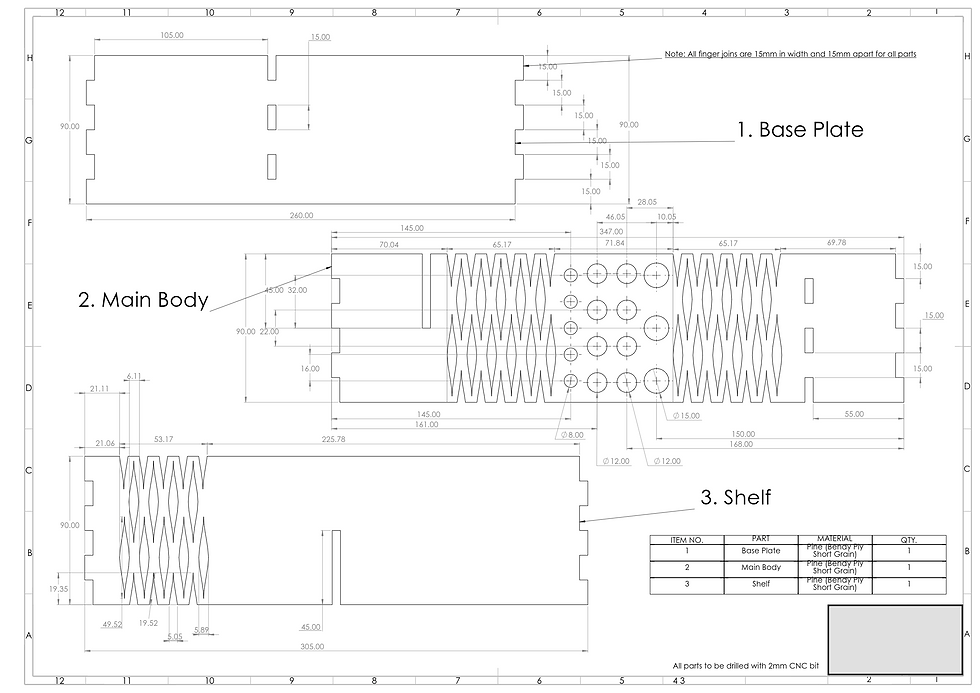

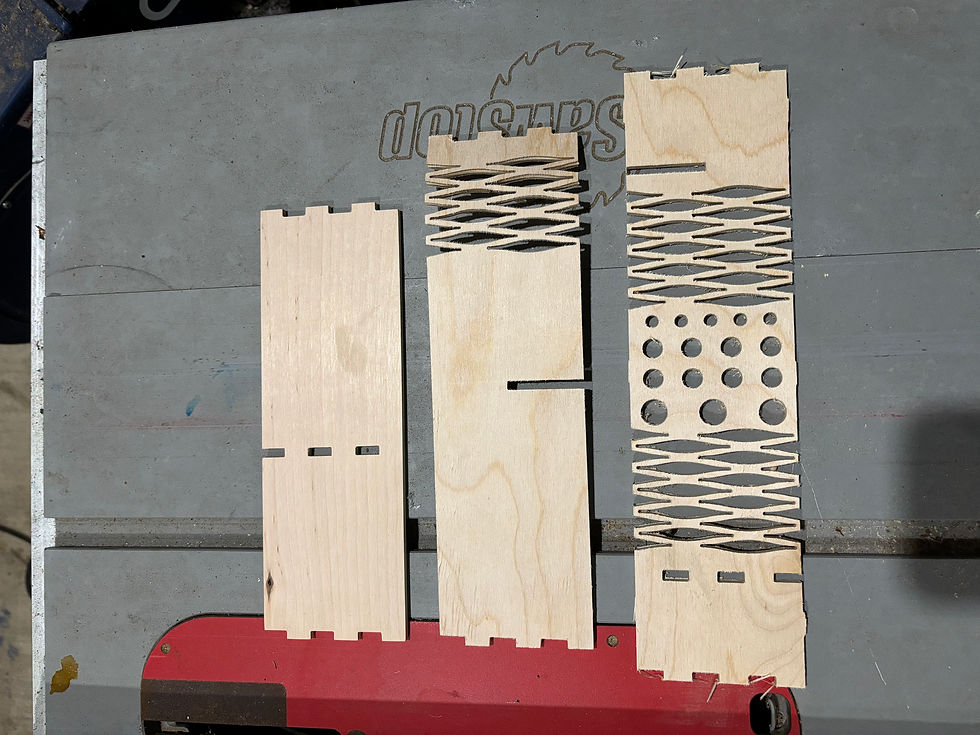
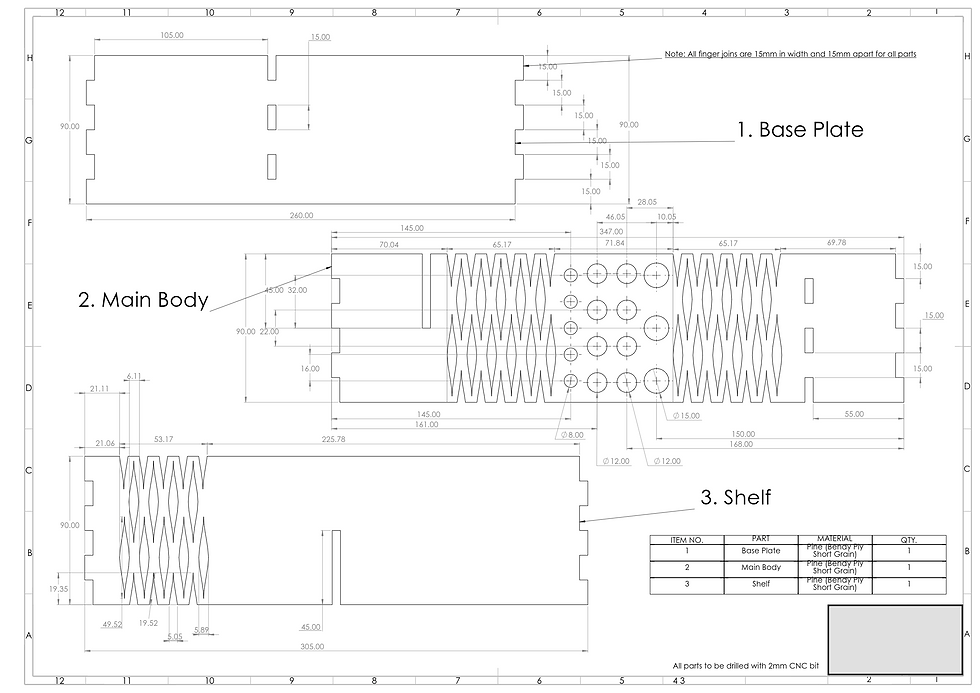
Final Product
The final product deviated greatly from my original design. I originally intended to laminate the bendy ply using a jig constructed from CNC. However, due to difficulty bending the ply, I attempted heat bending and half-cut kerfing along the interior of the design. The wood continued to break, and so I adjusted the design to utilise more significant honey-comb shaped kerfing. Furthermore, the design was split into three parts from the original two part system for easier assembly. Overall, despite the changes, the design can still be considered a success as it serves its function and still maintains the original asthetic appeal. All design requirements were also still met, with an emphasis on the simplistic and eco-friendly design.

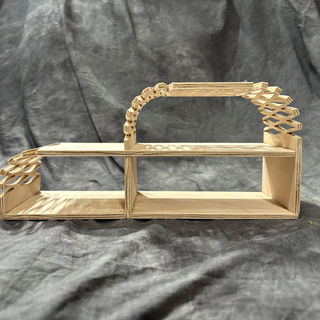
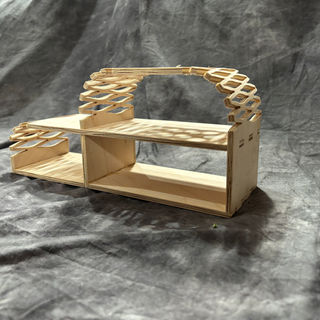

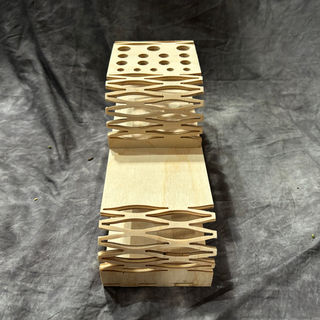
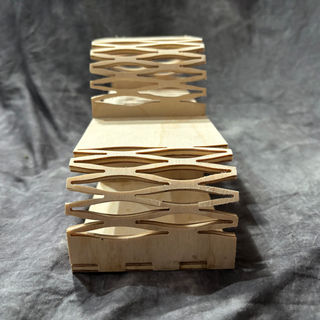