Tangram
Tangram is a stool that was designed for indoor seating within the Griffith University Southbank Campus. The design intent was to create a seat that could be easily moved and reorganised to cater for different group sizes. The tangram can be used individually or combined to form larger benches or tables. The adaptable nature of the chair hence promotes collaboration within the space but does not limit people who wish to work or seat individually. Sustainability was another key aspect of the project. It was ensured that all materials and manufacturing methods used were environmentally friendly.
Ideation and CAD
Various sketches were completed based on the design intent to explore different forms. The final design and how the different parts connected are showcased in the first sketch. The model was then recreated in CAD. Each part was created individually to allow for the files to easily transfer into CNC G-Code. The final image in the slideshow includes the assembled chair and its dimensions. The dimensions were achieved through ergonomics research and prototyping with cardboard and lower scale prototypes.
Research was also conducted into the different materials that will be used. It was determined that AA Marine Grade Plywood will be used as the primary material. The material is cost effective, whilst remaining aesthetically pleasing with a high-quality veneer on both sides. It was also ensured that the wood was sustainably sourced, confirmed through a PEFC certification. The joinery methods are friction fits with PVA wood glue to provide additional support. Finally, a shellac varnish will be used to protect the chair and provide a glossy finish to it. The varnish was also chosen as a natural and eco-friendly alternative to other varnishing options such as polyurethane.

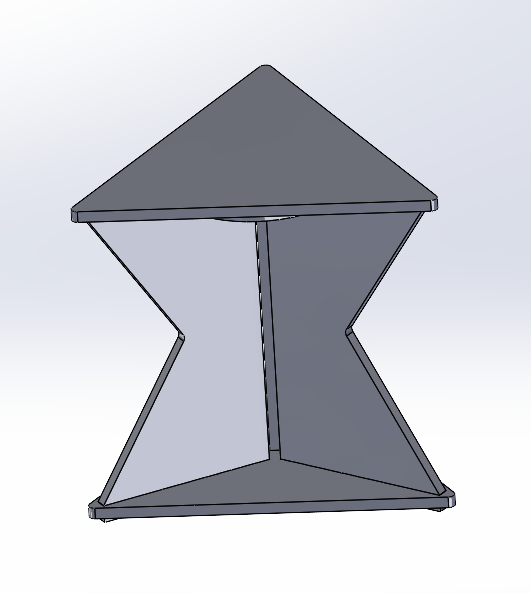


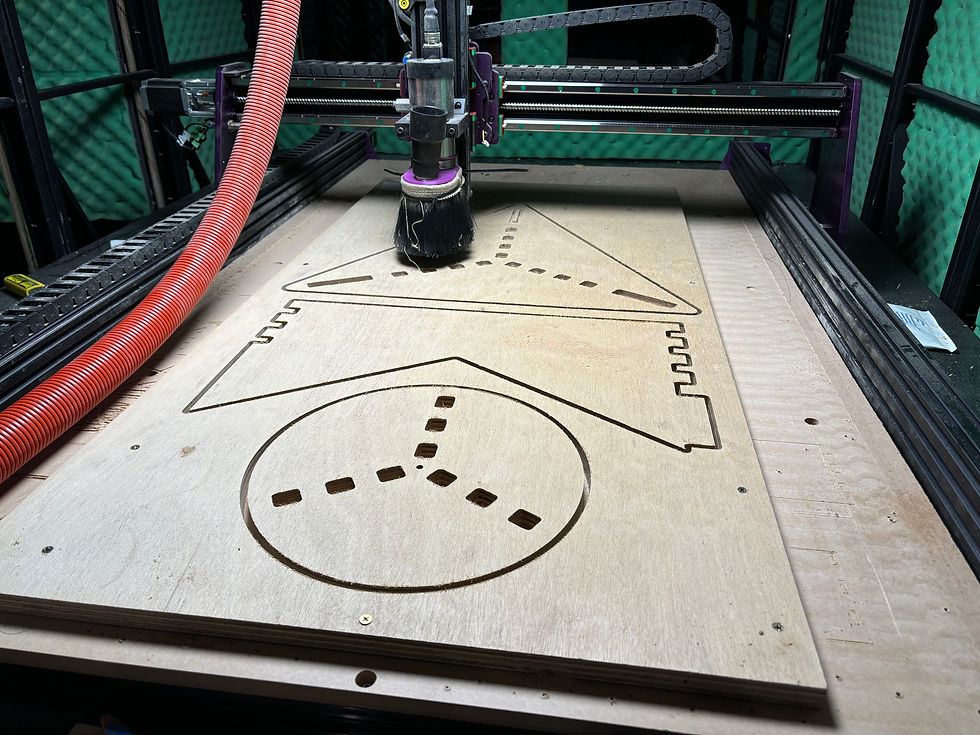

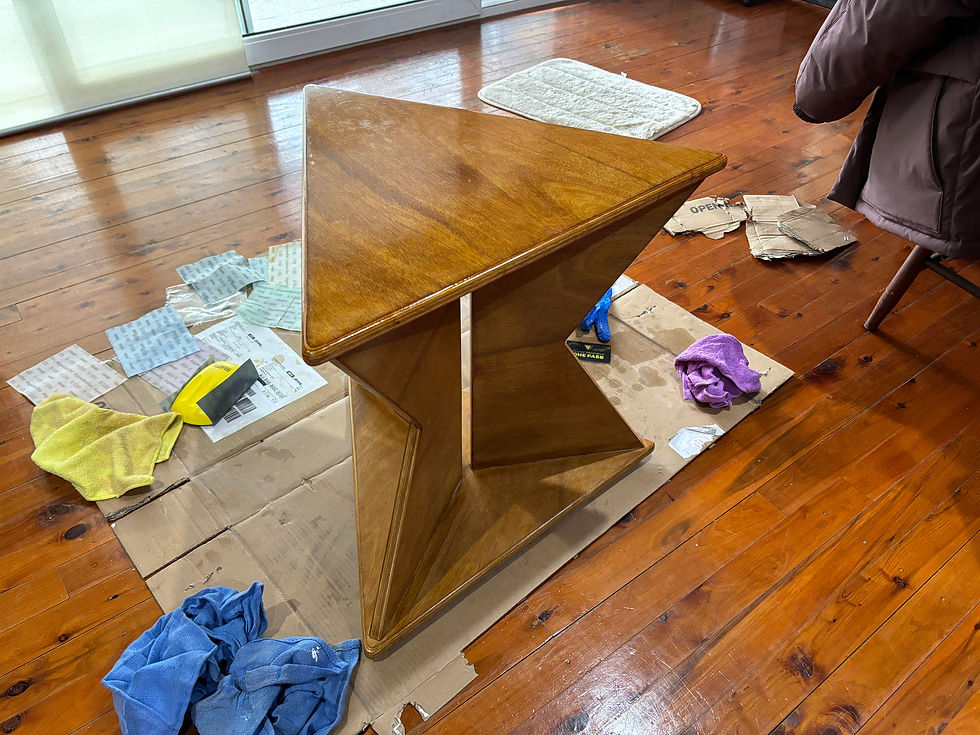
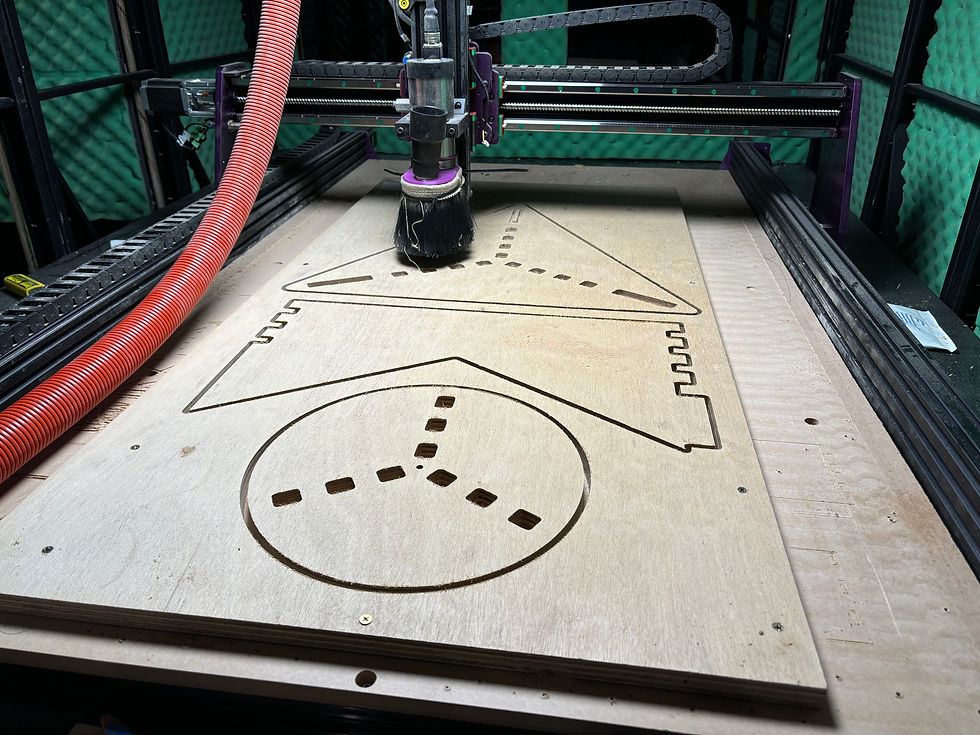
CNC and Woodworking
G-Code was created from the CAD files using ‘Carbide 3D’. The code was then uploaded to my CNC and was used to cut out the individual parts. These parts were then sanded with increasing grits up to 600p and the finger joins were filed to be square. The parts were then assembled using friction fit and wood glue at the finger joins. Wood filler was applied to all gaps and the excess was sanded away. The assembled model was cleaned, before varnishing with shellac. Three layers of shellac was applied to all surfaces, waiting five minutes between each layer. After an hour, the surfaces were lightly sanded with 600p. These varnishing steps were completed for a total of 9 layers for all surfaces and 15 layers for the top face. Finally, all surfaces were sanded with increasing grits of up to 3000p.
Final Product
The final product was effective in achieving the design intent of the project. It is relatively lightweight and can be moved and combined together cater to the user's need. The varnish was completed to a high level, creating an aesthetically pleasing glossy finish. However, I believe the stool would be more suitable for indoor use and potentially for a different demographic. A cost analysis revealed that the product would cost approximately $176 if produced individually and $109 each if batch produced as three. This is due to the material use and the labor intensive sanding and varnishing required. The chair may therefore not be suitable for a university demographic. To better align with the demographic, a cheaper material could be used and/or a more automated manufacturing method chosen to cut labor costs. Alternatively, a more durable, but less sustainable varnish such as polyurethane could be used to better protect the chair from damage.


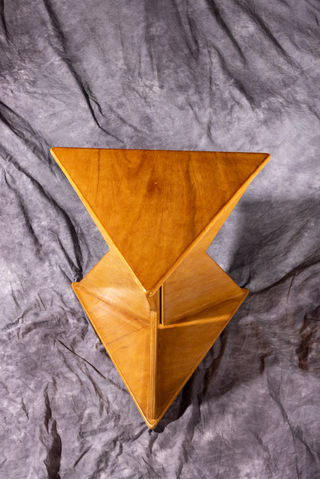
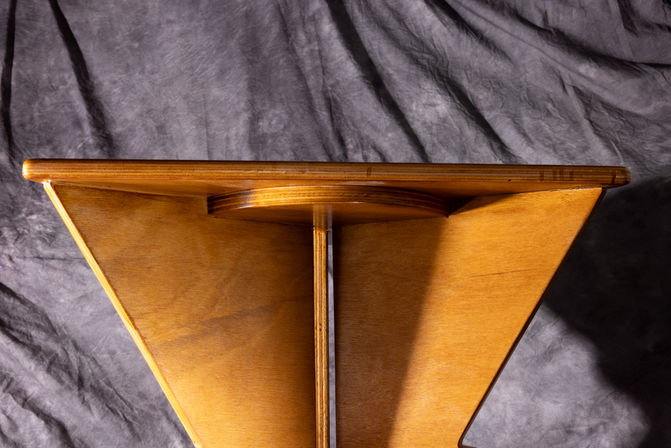

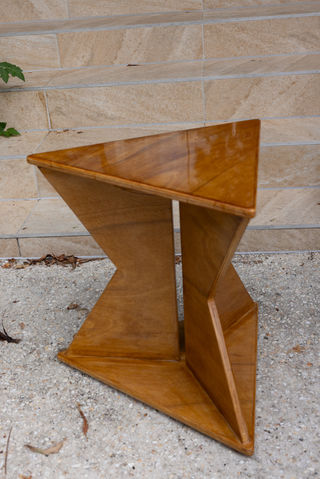
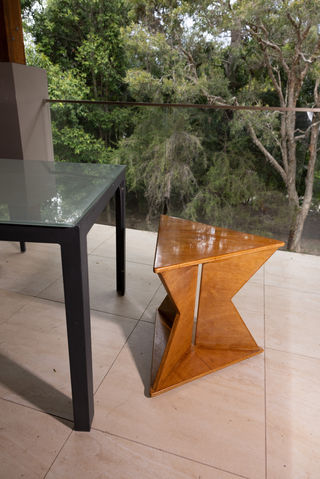
