BioSpine Placement
Summary and Reflection
BioSpine is a spinal cord injury (SCI) rehabilitation research project led by Griffith University. The project takes a unique approach of promoting neuroplasticity through cycling. The participant is positioned on an ergometer system and then placed in a virtual reality world. Their muscles are then electrically stimulated through the active thought of cycling.
I completed a 12-week placement at BioSpine and was given the role of the redesign of the foot-fixation system on the ergometer. A digital twin model has been developed for the program to help with supervision and ensure safety of participants. To align with the model, I must ensure the participants foot always remains at an approximate 90-degree angle. In addition, the device should cater towards the specific conditions of people with SCI. Limiting movements such as plantar and dorsi flexion as well as internal and external rotation of the leg were of primary concern. In addition, avoiding concentrated areas of pressure and minimising potential abrasion was a requirement. These criteria were developed through thorough research and collaboration with members of the team with specialised knowledge. I took on the role of an industrial designer for the project and was required to complete and document the full design process. My specific deliverables were to ideate and develop concepts that would function with a quick-release pin that was devised for the ergometer system. These should be expressed as sketches, progressing into rapid prototyping through 3D printing. I was then required to test and refine each prototype through self-evaluation and feedback from others. The final goal was to produce a high-fidelity functional prototype by the end of the placement that can be presented to the BioSpine team. I was advised that the problem was highly complex with no definite solution. The development of the system was however essential in optimising the ergometer system and any progression in the area would be highly beneficial.
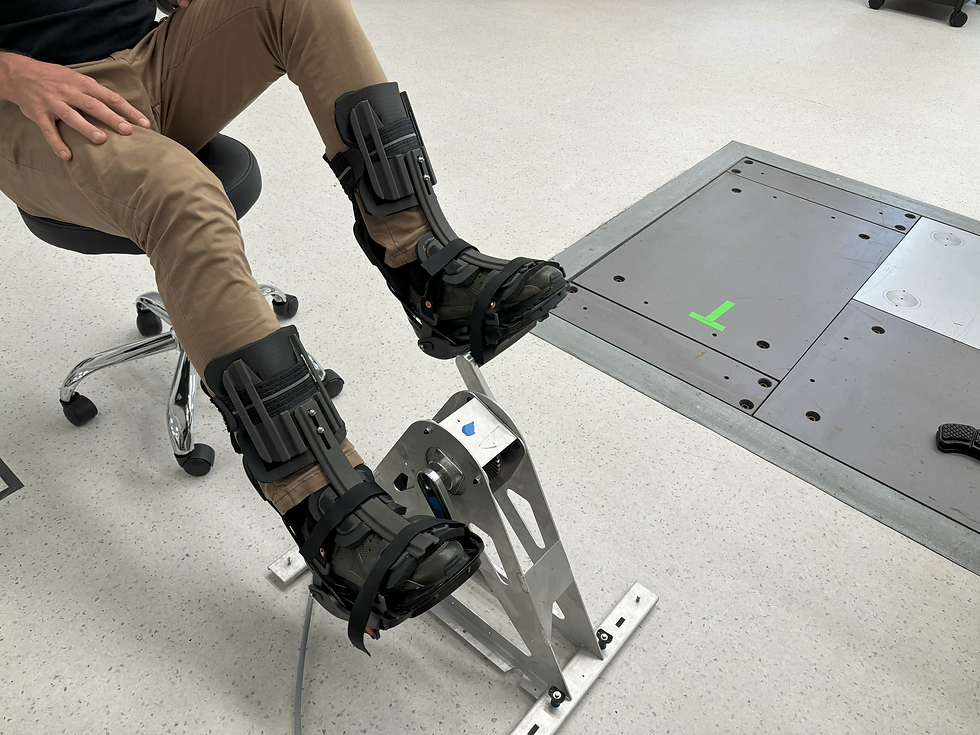
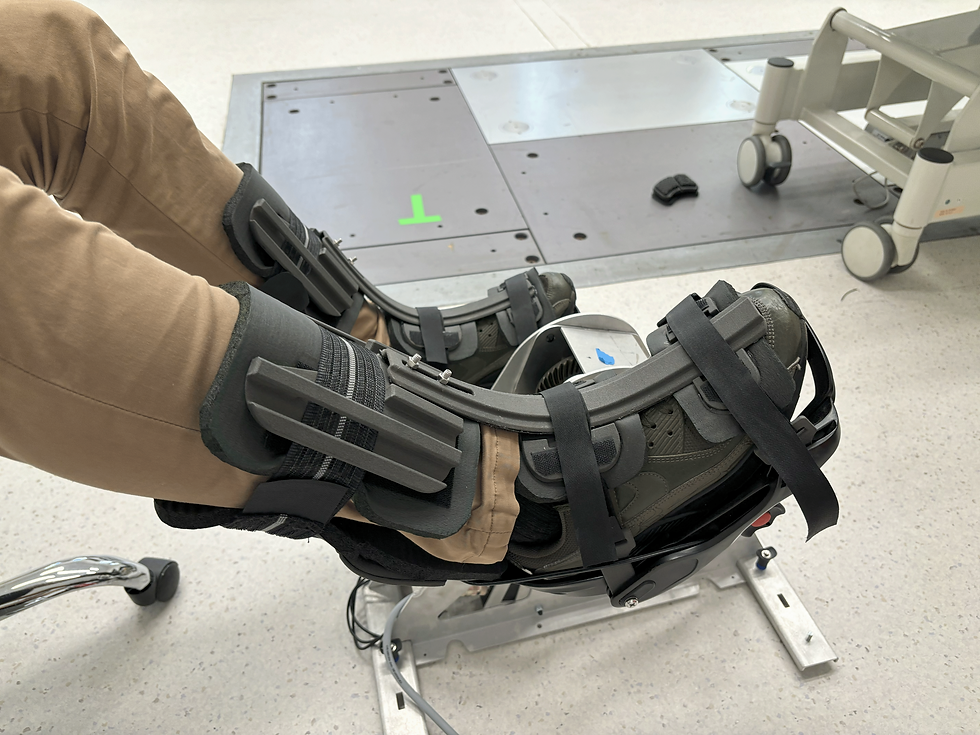

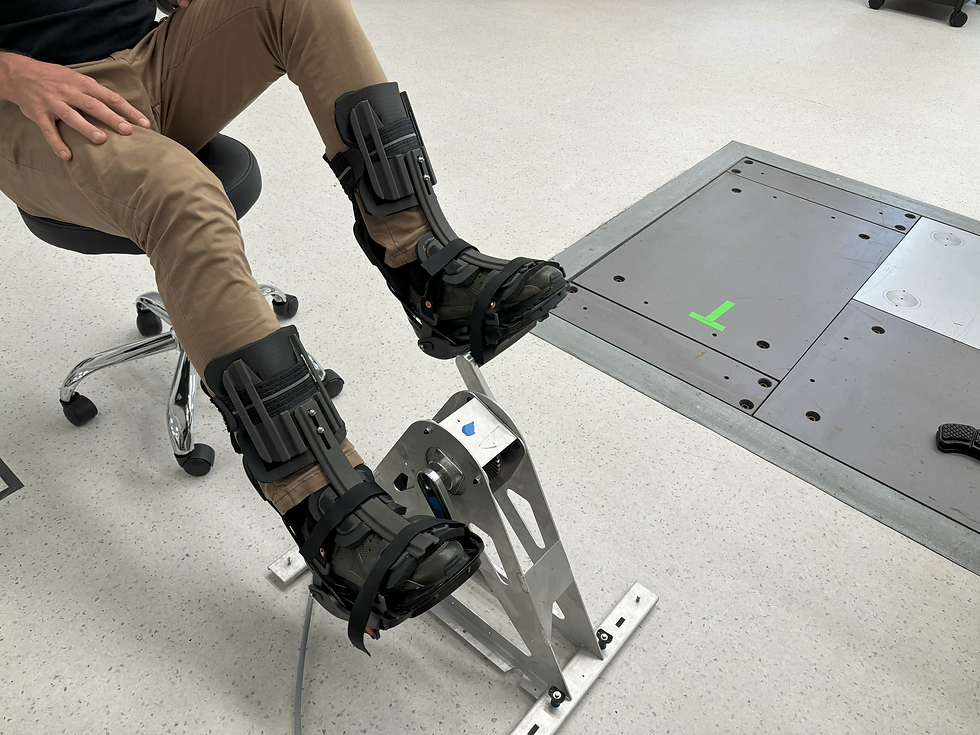
I utilised the first few weeks of my placement by researching and familiarising myself with the project. I learnt about SCI and the various limitations that the conditions present. Furthermore, I analysed previous attempts at the solution to identify their strengths and shortcomings. At the time of my placement, the intention was to utilise a snowboard binding which connected to the ergometer through a quick-release pin. The binding was easy to put on, where the back would fold outwards, allowing the foot to be placed inside. The backplate then snapped back, and the frontal binding could be tightened to match the user’s foot. It was determined that the base of the binding was quite effective, but the frontal binding straps did not provide the required support to prevent flexion and movement. The ideation stage would therefore revolve around the redesign of the frontal binding, which would interact with the existing base of the snowboard binding.



I developed a set of design criteria based off the research that would be used to guide the ideation stagE. Although ideas may be divergent in nature, these design rules helped determine how effective each solution was in potentially solving the problem and aid in selection for prototyping. During my research, I was inspired by a plantar-fasciitis splint, which wrapped around the user’s foot, with a rigid bar running from the toe to the knee. I purchased one and physically tested it to find that it effectively restricted dorsi and plantar flexion of the foot. The aspect of the rigid bar was greatly influential, where I would incorporate this element into my designs. The included sketch showcases an early iteration of the design but would evolve significantly throughout the design process. I then moved onto rapid prototyping, modelling the design in SolidWorks (CAD). My intention was to 3D print in PLA as a method of rapid prototyping. 3D printing is an essential tool in industrial design, as it can be used to quickly produce prototypes with low cost and minimal labour. Especially for the purpose of the project, I needed to create a custom design with freedom of form. The evolution of my design can be seen in the photos below. The design evolved greatly as with each iteration; various new problems presented themselves. For example, at the later stage, dorsi and plantar flexion was successfully mitigated, but internal and external rotation of the leg was still possible. To provide greater support in the leg region, the frontal binding needed to wrap around the back plate of the snow board binding. The back plate was not tall enough and required me to develop a separate part that connected to the snowboard binding to extend its height. The process of prototyping and reiteration is an essential skill in design, where one must be willing to receive feedback and adjust accordingly.



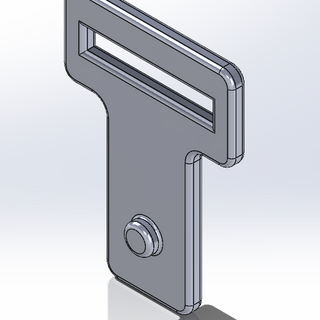


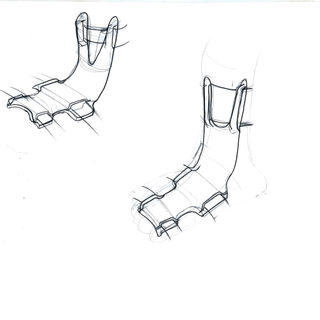

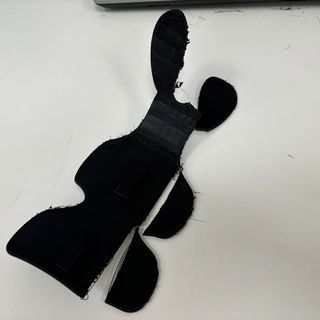
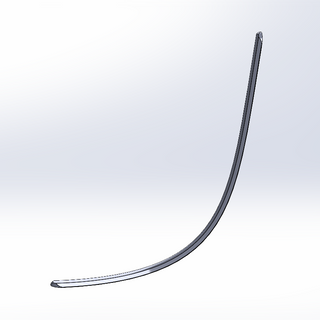
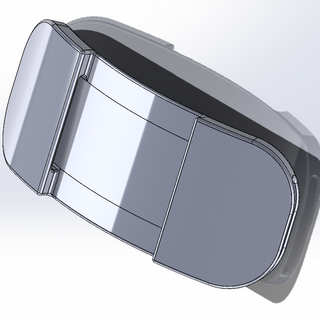
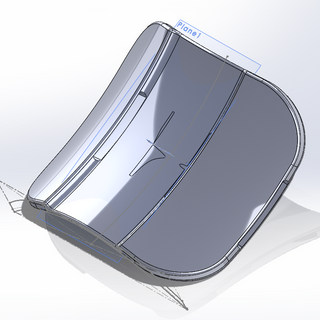



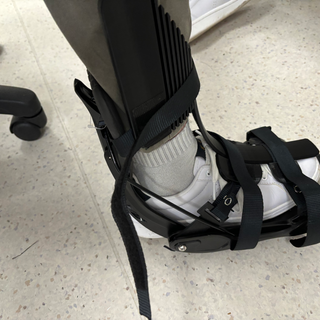
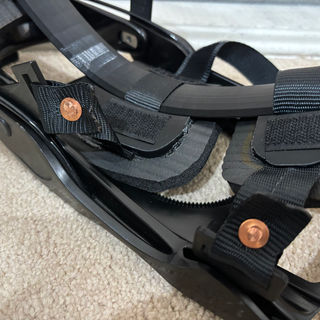
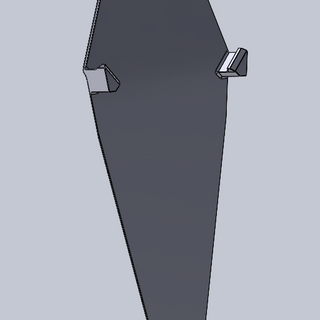

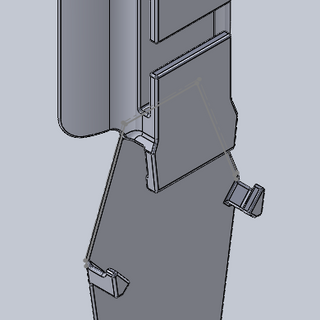
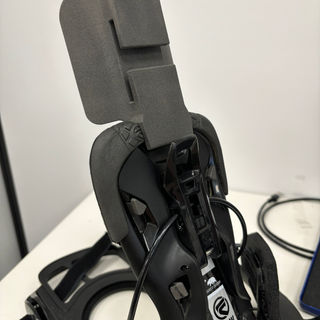
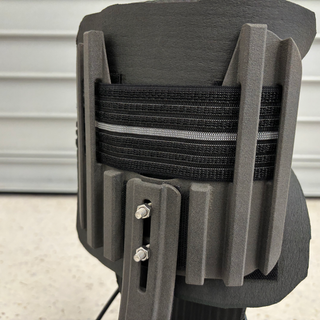



I was able to produce a high fidelity and functioning prototype by the end of my placement. Although pressured by time, I managed to perfect the form of the foot-fixation device in PLA and complete higher quality prints in my chosen material of nylon. The material offered greater precision and strength. I was able to test the design on the ergometer system, revealing that the device was highly functional and achieved all set design criteria. The foot was firmly secured by the frontal straps and foam padding ensured that there were no concentrated areas of pressure. The foot is kept at a 90-degree angle with limited ability to internally and externally rotate the leg. Improvements can still be made to the accessibility aspect, where the device could be difficult to put on. The observations were supported by feedback from my supervisor and the team, who agreed with the success of the device. However, there is still room for refinement, the binding will provide a solid foundation for future progress in development of the foot-fixation device.
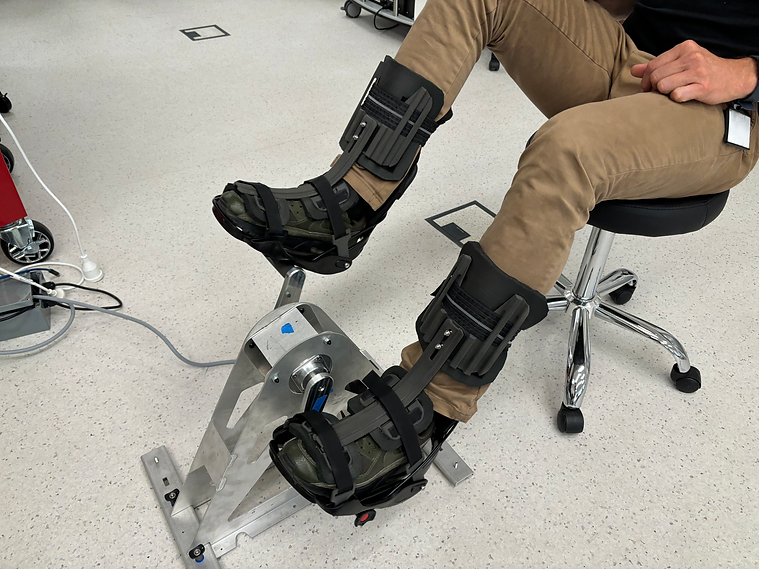
My placement at BioSpine has helped me significantly improve as both an industrial designer and an individual. My deliverables directly aligned with the typical design process of an industrial designer. I was able to effectively research and produce high quality concepts. Sketching has previously been a weakness of mine, as it was a skill I had not consistently practiced. Evan, my supervisor prompted me to keep sketching and we both noticed great improvements in quality over the placement. I was able to transfer these concepts into CAD models to be 3D printed for rapid prototyping. Formerly I would utilise cardboard modelling as my primary method of prototyping. The project however required greater precision and customisation, achievable only through 3D printing. I believe my skills and knowledge about this manufacturing process has improved greatly as a result. These technical skills will further boost my employability as an industrial designer. Finally, the placement has taught me the importance of taking initiative. I believe I am a perfectionist in nature and was afraid to make mistakes. This would hinder my critical thinking and ability to simply try new things. Evan noticed this and taught me that making mistakes is part of design. By the end of the placement, I believe I showed greater initiative, always attempting something, regardless of the outcome.
